
This understanding comes from analysis of specialized graphs, such as Bode, root-locus, and Nyquist plot, which build intuition of how the plant will behave. When designing a controller it is best to fully understand the plant, in our case, the DC Motor. The next step is to choose a control method and design a controller. The MathScript node can be found under the Programming > Structures palette.
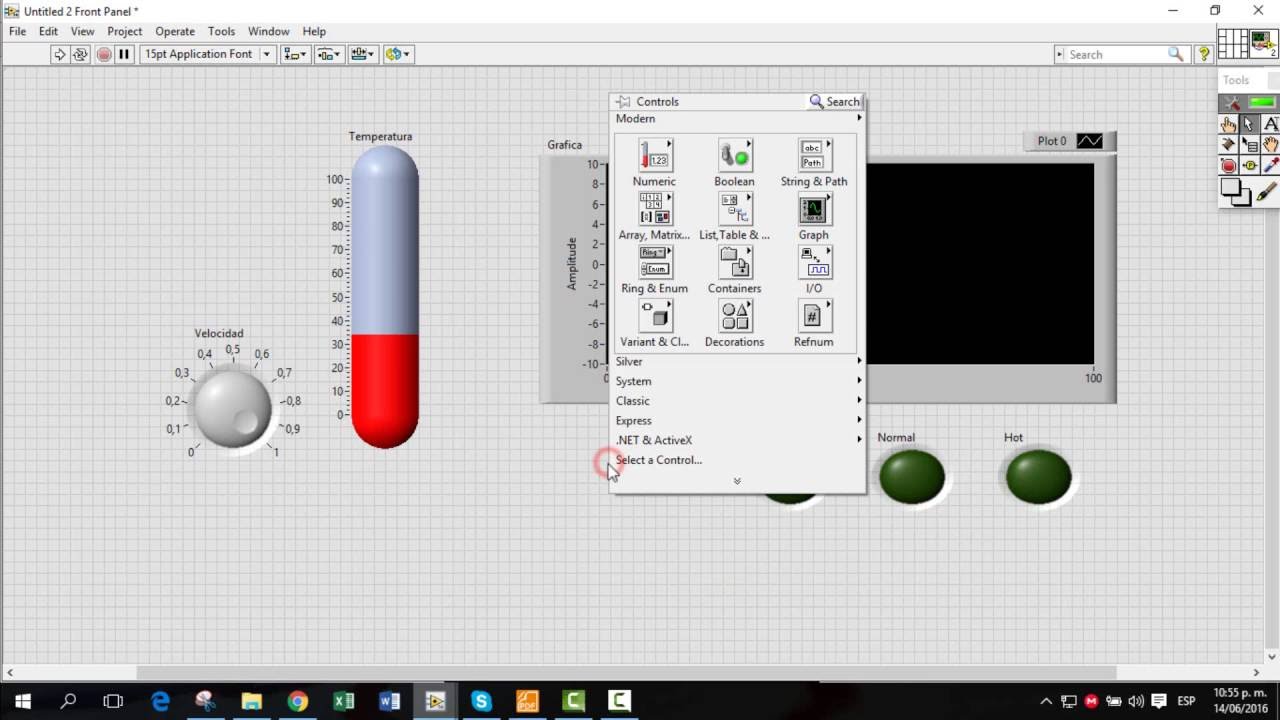
Model of the DC Motor represented in the LabVIEW MathScript Node We can represent this transfer function in LabVIEW by using a MathScript Node which is part of the LabVIEW MathScript RT Module. The input parameter values were obtained from the Quanser QNET DC Motor specifications sheet.įigure 2. This model will be used to design a closed-loop controller, which can then be tested with the actual motor. Mathematical Model or Transfer Function for a DC Motor Jeq = Equivalent moment of inertia (kg*m2) (Assume that Jeq=Jm(Motor armature moment of inertia))įigure 1. We can use the equation below to represent the model of our DC Motor where: In our case, the input to the system is voltage (V m) and the output from the system is angular velocity (Ω m). A transfer function provides a mathematical description for how the inputs and outputs of a system are related. The DC motor can be best represented by a transfer function. For this experiment, we are going to create a model for a DC motor. Many types of systems can modeled, including mechanical systems, electronic circuits, analog and digital filters, and thermal and fluid systems. The first step to designing a closed-loop controller is to identify a mathematical representation of the plant, or create a model.
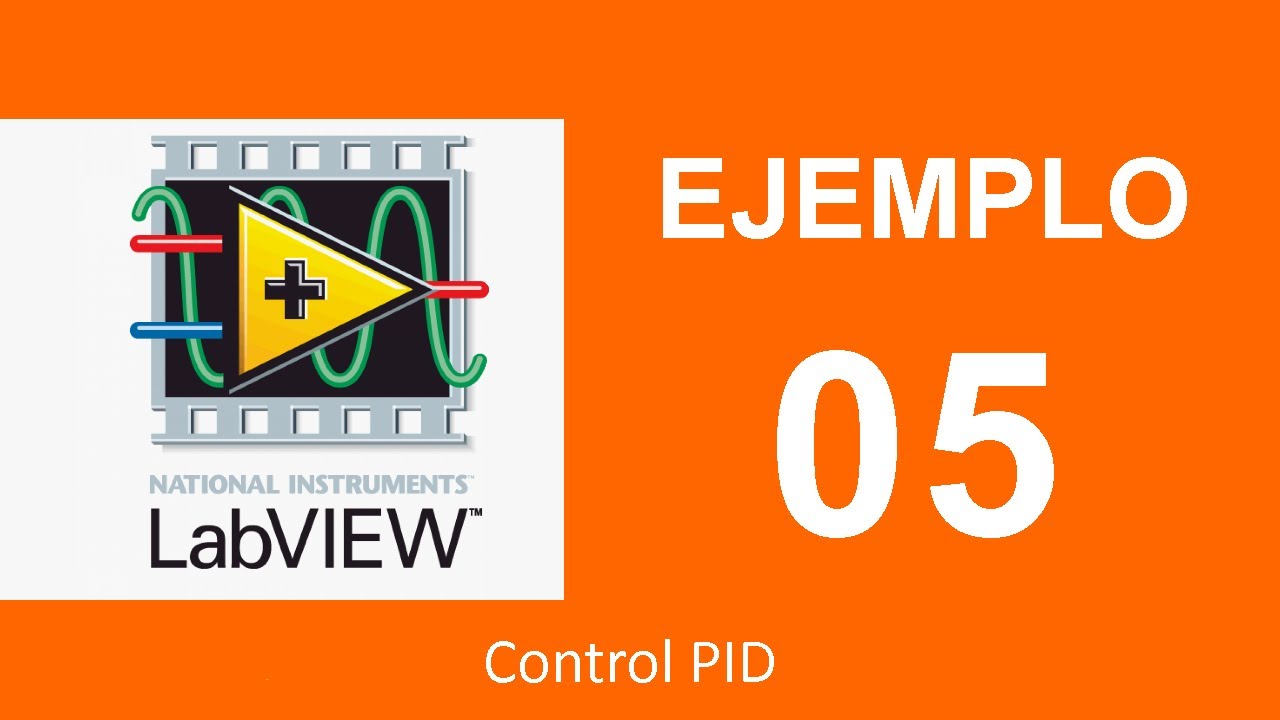
The concepts of control are essential for understanding natural and man-made systems.
